During World War II, auto plants stopped making cars and instead churned out tanks. Factories designed to produce washing machines retooled and started manufacturing aircraft parts, and clothing manufacturers turned out uniforms by the millions. That’s what a country does when it faces an existential crisis.
Now there’s another crisis: the coronavirus pandemic that has already killed thousands of Americans and tens of thousands around the globe. And like the crisis the country faced in the 1940s, the pandemic caught the U.S. unprepared, short of even the most basic equipment needed to protect healthcare workers, first responders, and vulnerable individuals.
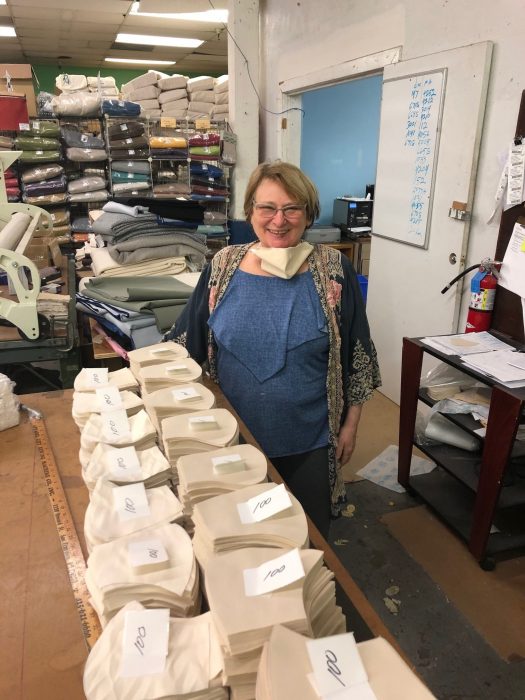
And that’s where Suzanne Diamond, the 65-year-old founder and CEO of the San Francisco-based Futon Shop, comes in. Realizing that masks are in critically short supply, Diamond decided to shift production at her factory and showroom on Cesar Chavez Street from futons, mattresses and pillows to masks. “People on the front lines are dying, the elderly are afraid to go out, they have no protection. I felt horrible and I needed to do something,” she said.
Diamond’s team of five sewers and two helpers cranks out a triple-layered, cotton mask every 90 seconds. That amounts to about 600 a day, but it’s not nearly enough to meet demand. “I have orders for thousands,” said Diamond, who sounds — and freely admits — to being somewhat overwhelmed by the pace. “I’m exhausted; I can’t keep up.”
Orders have come from the Department of Transportation, for its bus drivers; national parks, for their staff; as well as businesses preparing to re-open, from restaurants to country clubs to ice cream parlors. All of the orders have been generated by the company’s web site, which people come across when they do a search for cotton masks. “I haven’t spent a penny on marketing,” she says.
Although mask making is a new skill, working with fabrics, said Diamond, is “in my DNA.” She comes from a New York family that started what she believes was the first chain of tailor shops in the United States – the Five Little Tailors — and her father was a textile designer.
Why start a futon business? “I was a hippie, into things like macrobiotics and thought I should be sleeping on natural fibers,” Diamond said. Her first futon was made for her son, born in 1976. “At the time, you couldn’t find anything organic.” Most baby bedding had chemicals or fire retardants in them, she said.
She founded the Futon Shop that year and the business has grown to include 10 showrooms in the Bay Area and Southern California.
Diamond speaks with a New York accent — she grew up just north of New York City — and comes across as a kindly grandmother – which she is. She spends as much time as she can with her two grandchildren and has provided employment for family members over the years.
The switch to mask making also fills a gap in futon sales. Pandemic restrictions forced her to close all her showrooms. For the protection of staff at her San Francisco showroom and factory, she’s reduced her workforce from 43 to seven employees. Many of these employees are using personal time while off duty.
Although she’s feeling the stress of sourcing enough materials to meet demand, she said she’s happy to be doing something creative. “I went to art school. I like to create things.”
It took seven tries to find a design for the mask that was relatively easy to manufacture and comfortable for people of various sizes to wear. “We tried it on different faces, different size heads, on big noses and small noses.” Diamond said. Finding the material she needed was easy. “I’m in the mattress industry; everyone is looking for something unique.”
The masks sell for $16 to $23 each, depending on the style and the quantity purchased. For each mask she sells, Diamond donates one to nonprofits, which then distributes the masks to homeless shelters, nursing homes and other needy groups. Some go to hospitals, but the masks are not medical grade, something Diamond hopes to change.
She’s sent samples to a testing lab in Utah in hopes of winning certification for the masks as a medical device.
Her masks are more complex than you’d make at home. The outer and inner layers are made from a closely woven cotton. One version includes a middle layer made from a fabric with copper filaments woven in. Researchers have found that copper is an inhospitable environment for viruses, which is why some experts recommend that it be used for doorknobs and other frequently touched surfaces rather than stainless steel. There is also some evidence that infusing a mask with copper may form a barrier viruses have difficulty penetrating, though it has not been proven.
She’s still selling futons, but only online. A few staff are still making futons – her factory has all the heavy duty equipment needed to make them, even those that churn imported wool and cotton into bats (sheets) for making futons. But most of her staff is busy taking orders for face masks now.
Demand is so high that Diamond is now outsourcing some of the work to a factory in Los Angeles and is negotiating with producers in other states and even Tijuana. And she had to find a new source for the copper-infused cotton – in Brazil. Suppliers in Pakistan, India and Turkey are no longer available.
Like many other seniors, Diamond is coping with high levels of fear and uncertainty. But making the masks “makes me feel like I’m not just waiting for someone else to have a solution. I’m doing something to help.”